Weight: up to 28 ton. Length: up to 19 m
Our kettle:
- length 16.5 m
- width 2.8 m
- depth 3.4 m
These dimensional ratios allow the processing of large elements (maximum Hot Dip Galvanized lengths 19 m with weight up to 28,000 kg) with high quality standards.
Are you interested in this type of processing?
Watch the video
Dimensions, weight
and geometry
Dimensional limits in the Hot Dip Galvanizing sector have been overcome in recent years with galvanizing kettles which allow the dipping of elements with exceptional dimensions.
That must also to be added on the increasing capacity for handling elements with weights greater than 25t.
These dimensions gives the opportunity to consider Hot Dip Galvanizing even on product that until now, have not been possible to do.
The most affected sectors are infrastructure (bridges and construction) and miscellaneous plant engineering.
The guaranteed anticorrosive performance of Hot Dip Galvanizing, added to the chance of galvanize big dimensions, can open up new horizons to design choices.
It is fundamental the collaboration between designer, metallic producer, and galvanizer to face new goals.
Example of hot dip galvanizing
of exceptional pieces
Vadena highway overpass on the A22 Brenner freeway
Dimension of the overpass:
Length 47.20
The metal structure, by choice of the final client, was to be hot-dip galvanized and painted.
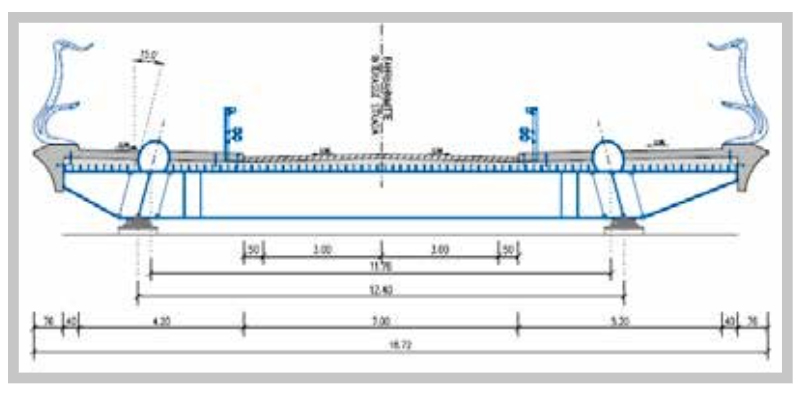
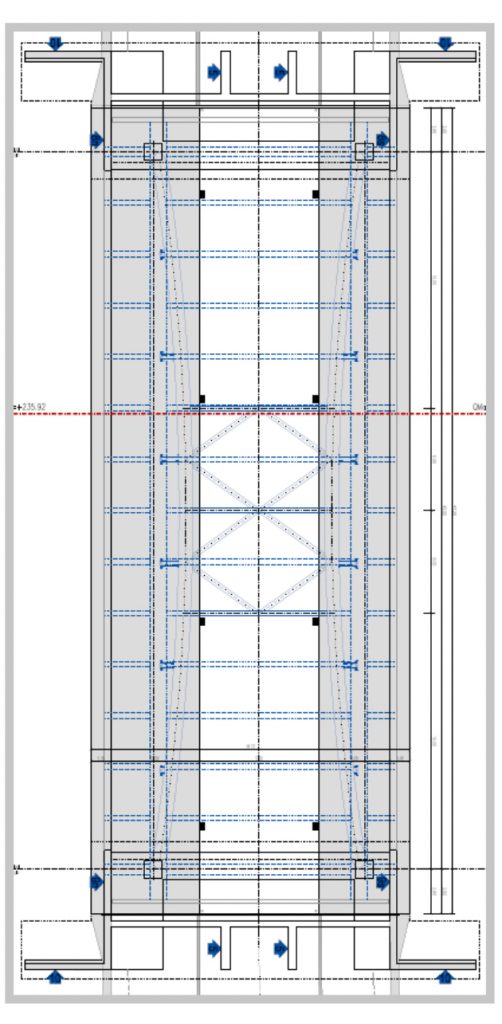
Feasibility Study
Subdivision of the bridge into elements by size for Hot Dip Galvanizing
Evaluation of the dimensions to minimize the number of elements that must be welded on-site.
Choice of steel for Hot Dip Galvanizing suitability
Research on the market of mechanical properties steel and chemical characteristics suitable for Hot Dip Galvanizing
On-site welding operation of section.
Protection of the edges segments to provide to welders no-zinc surfaces.
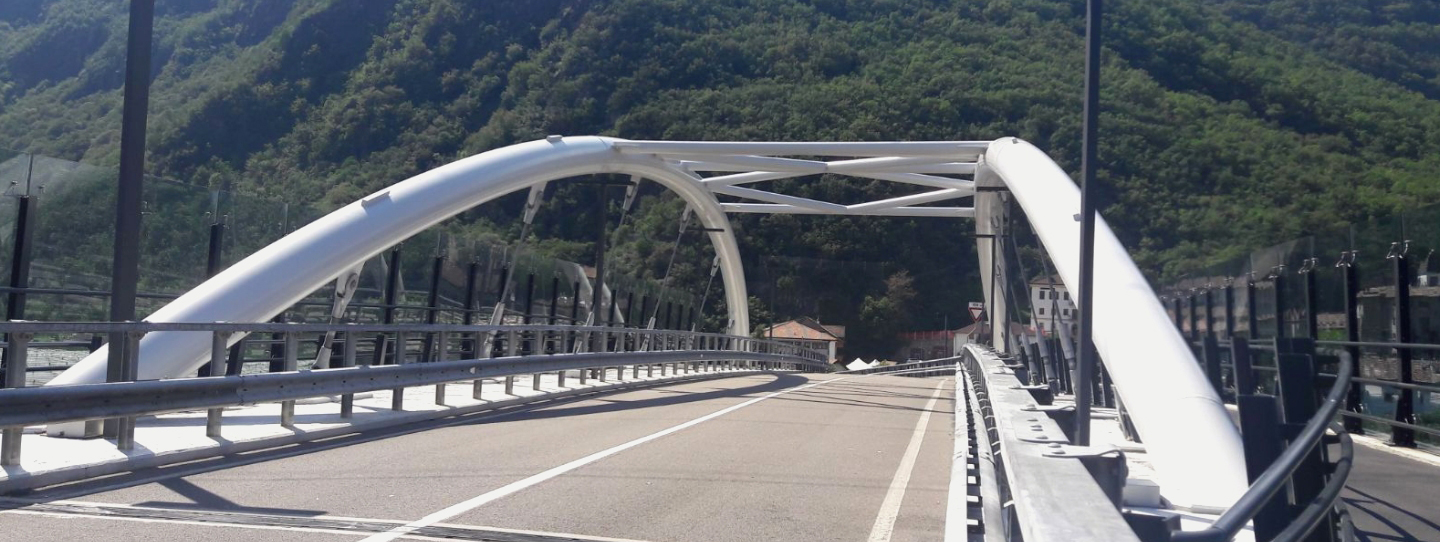
Subdivision of the bridge into elements by size and weight
Each of the two main beams of the bridge, following the discussions between designer – metallic producer – galvanizer, was divided into 3 elements with a maximum size of 2710 x 2207 mm, with a length of about 15000 mm. Each element of the beam weighed between 20 and 22t.
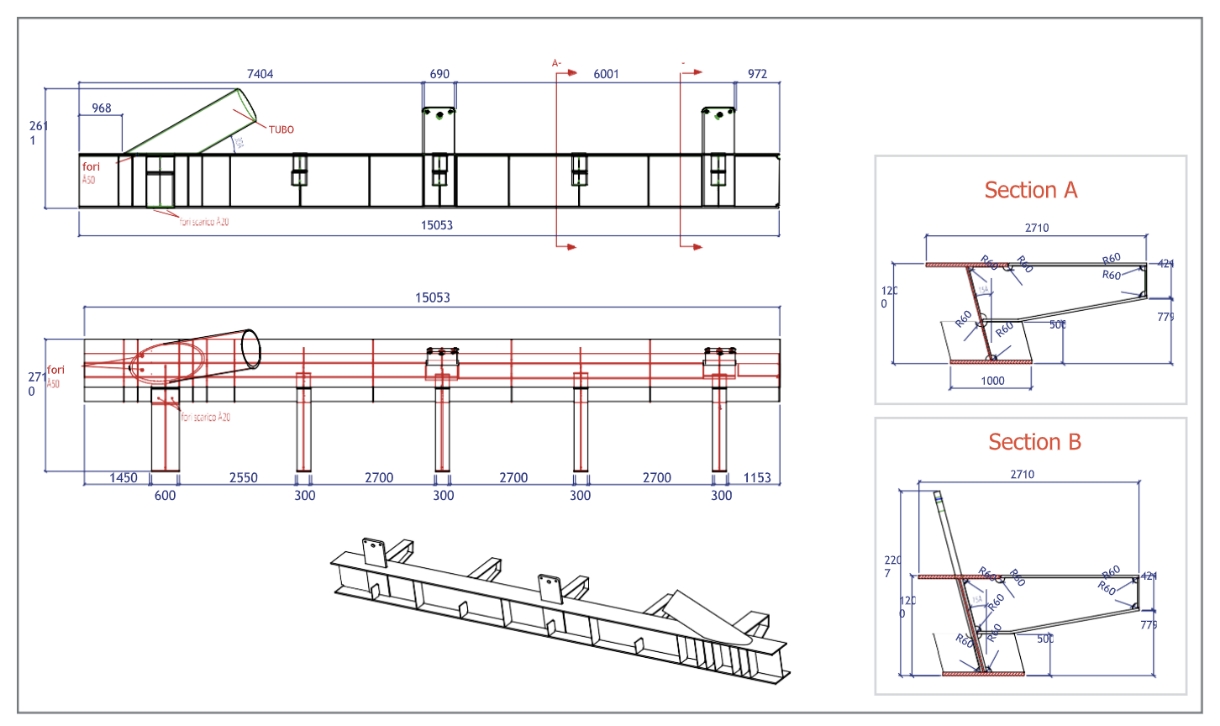
Choice of steel for Hot Dip Galvanizing suitability
The welded beams of the bridge were constructed using steel sheets with 20 – 40 mm thickness. The choice of steel, suitable for Hot Dip Galvanizing is fundamental, especially on these elements. The mass of each element is such as to require very dipping time (20 minutes against the normal 2÷5 for simple materials). Time of dipping very high cause very high thicknesses of zinc layer which give high anticorrosive performances but are also extremely fragile.
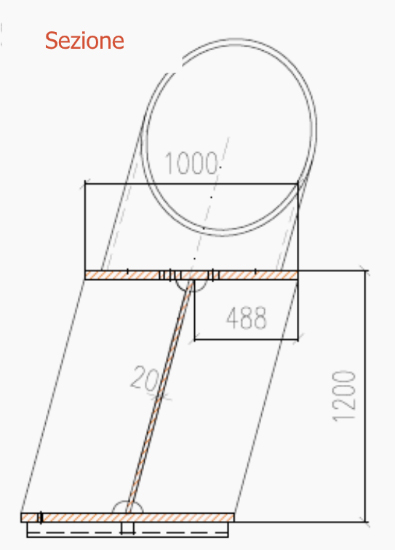
On-site welding operation
of segments
Welding Hot Dip Galvanized profiles is not recommended. To enable this operation on construction site, a certain paint was therefore used in the points intended for coupling: the paint creates a barrier against the formation of the protective zinc layer, leaving the area substantially raw. Below you can read the procedure that was established specifically for this project.
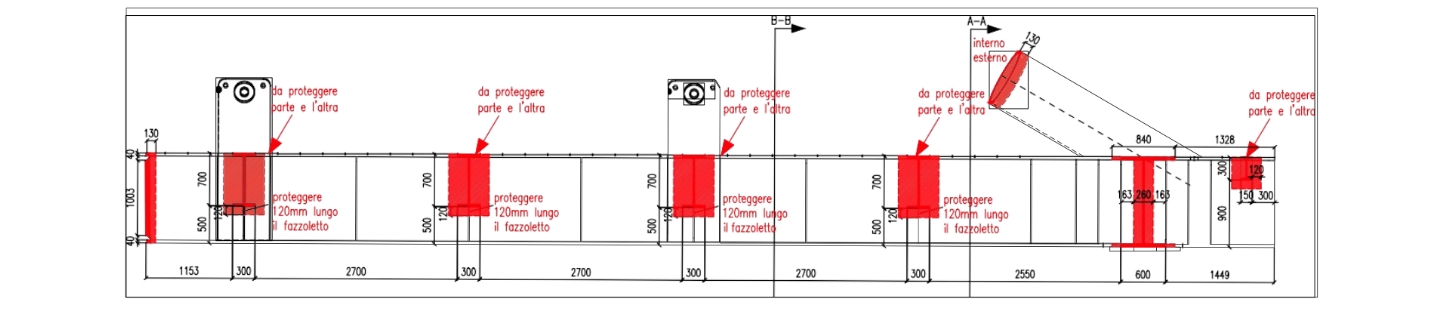
Vadena Bridge
General procedure for the protection of areas that must be welded on construction site:
1. Identification of the areas involved in the protection treatment with paint to avoid the formation of the zinc layer.
2. Mechanical cleaning of the areas indicated to apply the paint.
3. Applying of antizinc paint (e.g., W&S Antizink) on the indicated areas. The function of the substance is to create a barrier on the steel to prevent the adhesion of the protective Fe-Zn alloy.
4. Hot Dip Galvanizing treatment.
5. Mechanical cleaning of the affected areas to eliminate paint residues.